Prevent vehicle downtime with predictive maintenance
Mechanics are proactively informed of future technical problems and maintenance needs within your fleet. Our solutions monitor all vehicles remotely to prevent breakdowns and consequential damages.
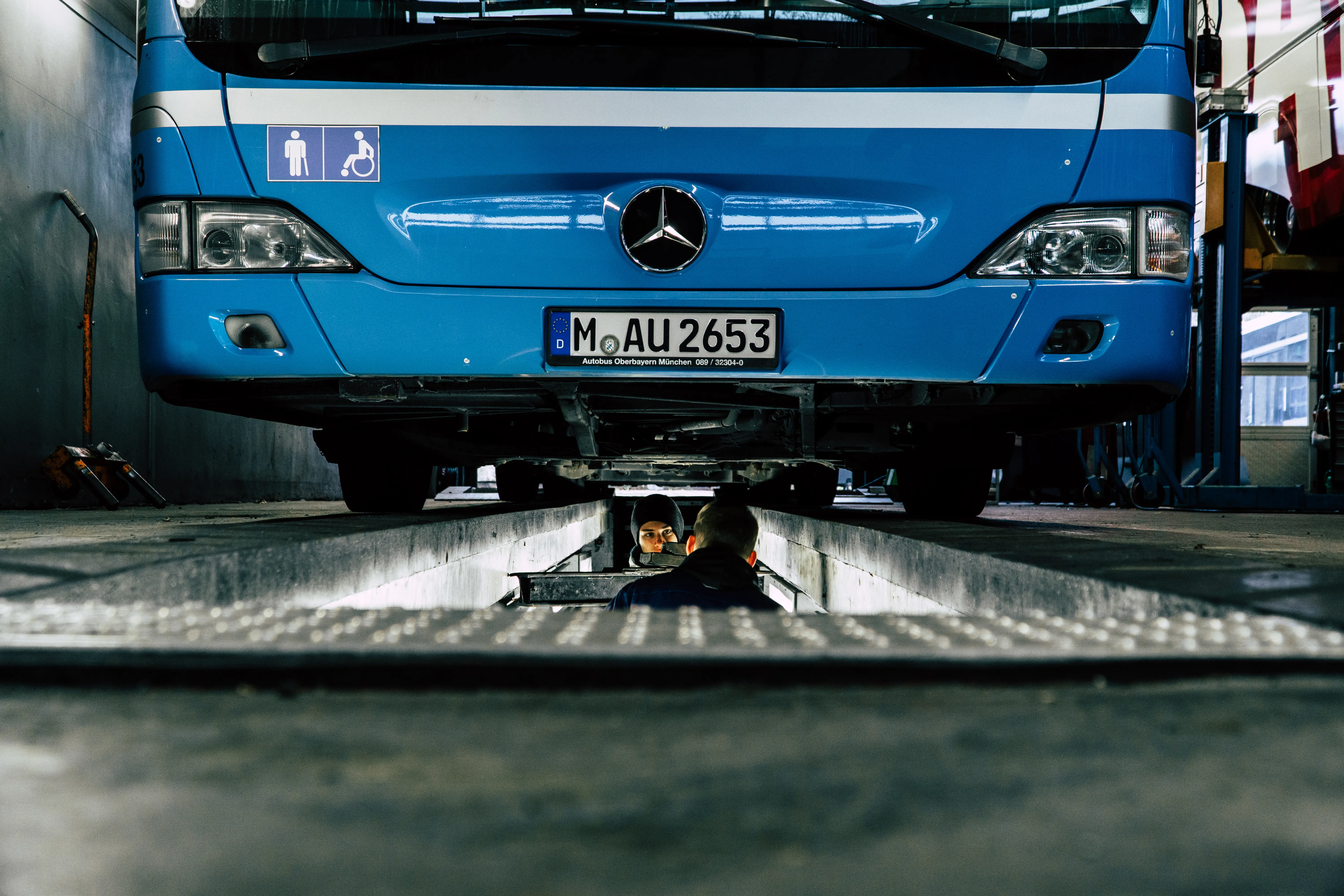
Trusted by leading mobility providers
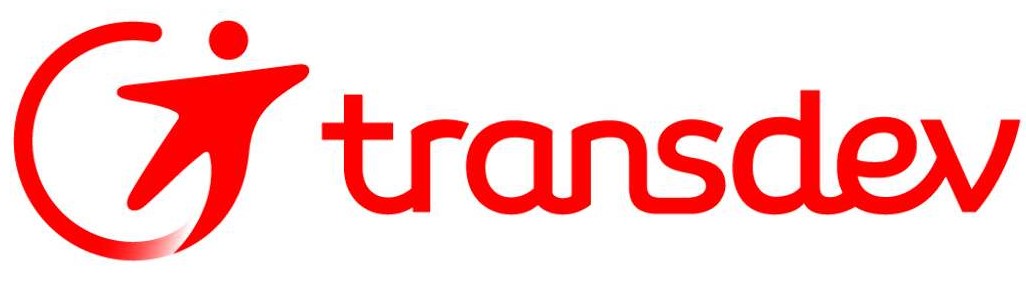
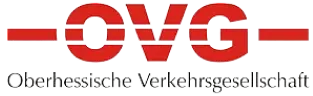
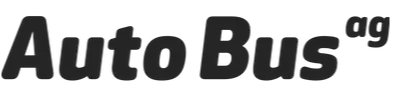
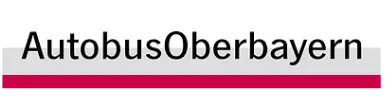
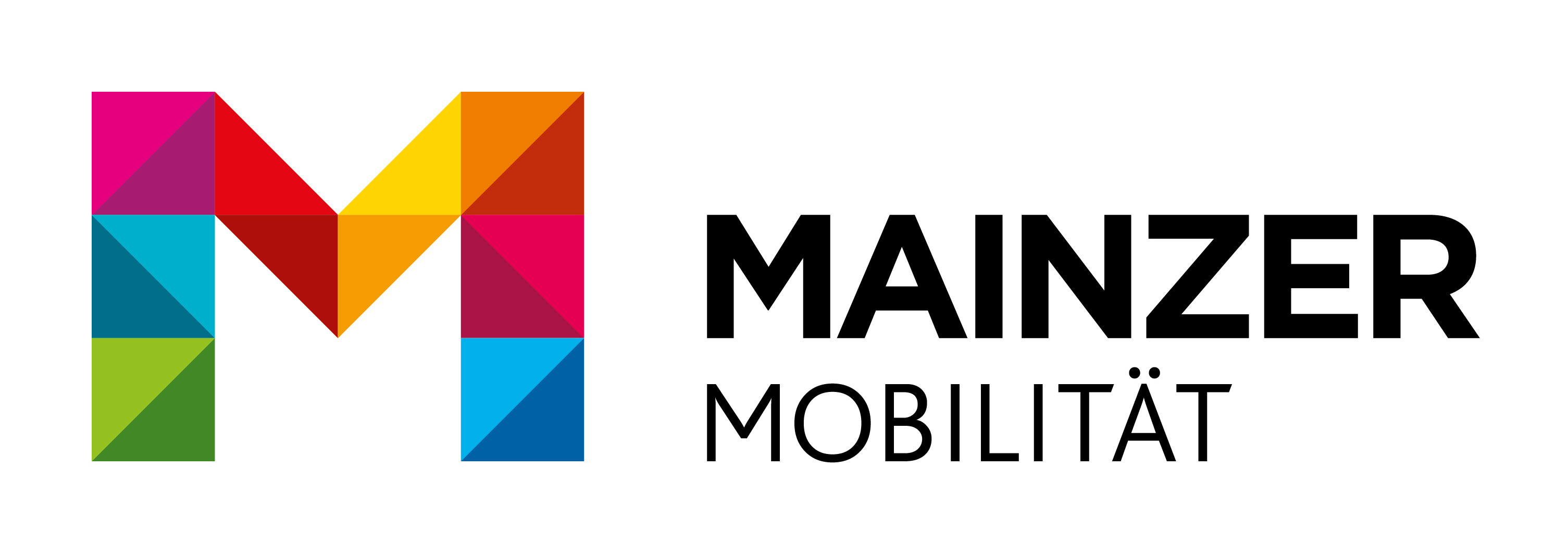
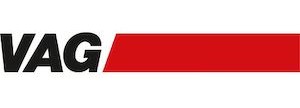
Achieve reduced vehicle downtime by planning ahead for technical problems
Buses and trucks come for maintenance in regular intervals. However, these workshop visits are only snapshots of the reality and cannot uncover all health issues. The only way to reduce unplanned vehicle downtime is the constant real-time monitoring and analysis of technical problems. Mechanics need to be made aware of irregularities within the fleet before they lead to operational disruptions.
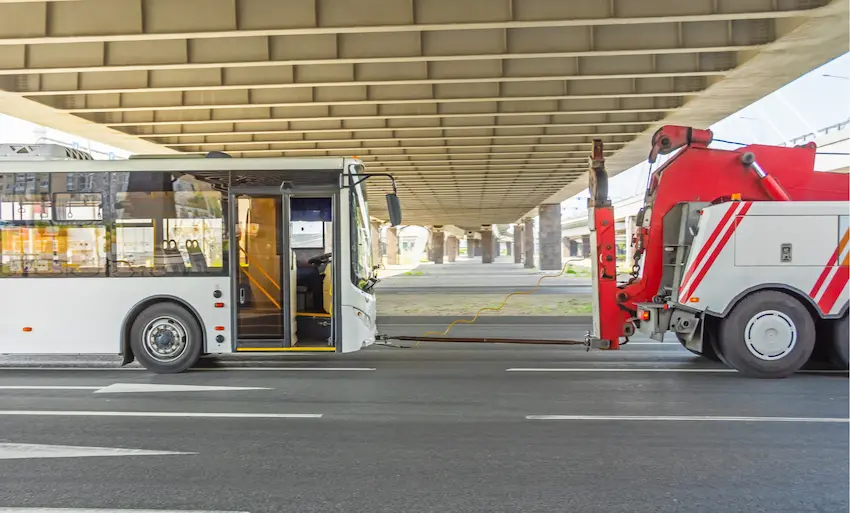
Before: Flexibility and reserve capacity are essential
- Vehicle replacements during operation due to questionable vehicle health
- Unplanned workshop visits due to sudden faults
- Long downtime duration for serious damages
- Long wait time for spare part orders due to supply chain interruptions
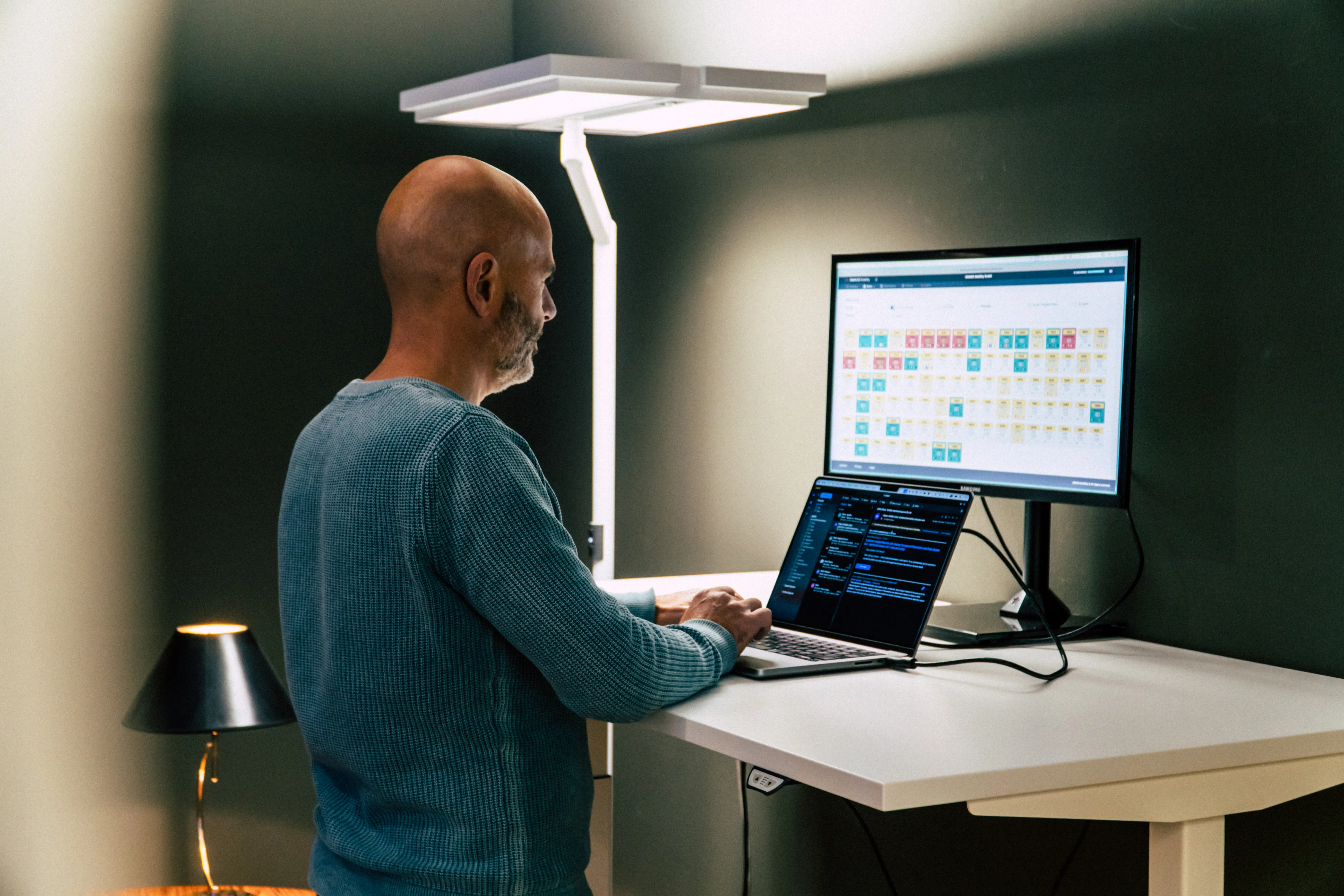
After: Unplanned downtime is reduced to a minimum
- Vehicle replacements are reduced as only healthy buses are put into operation
- Unplanned workshop visits are reduced due to remote assessment of fault severity
- Serious damages are reduced through early intervention triggered by proactive alerts
- Transparent vehicle conditions allow just-in-time spare part orderings
We increase availability and maintenance efficiency of commercial fleets.
Our platform serves diverse needs in vehicle maintenance and planning, fostering effective communication among stakeholders. With continuous updates and innovative features, we strive to elevate the experience and empower all involved, ensuring a dynamic and collaborative environment.
Remote Diagnostics
- Receive and delete all fault codes with translation and severity
- Resolve problems swiftly, reducing disruptions
- Reduce frequency and duration of unplanned workshop visits
Predictive Maintenance
- Anticipate and address problems before they disrupt operations
- Minimize downtime and reduce overall maintenance expenses
- Prolong asset life through timely interventions
Condition monitoring
- Detect issues early to avoid costly downtime
- Enhance equipment longevity through proactive monitoring
- Reduce repair expenses with preventive measures
Alarm for critical events
- Swift Reaction to Urgent Alerts
- Prevent accidents, breakdowns and replacement
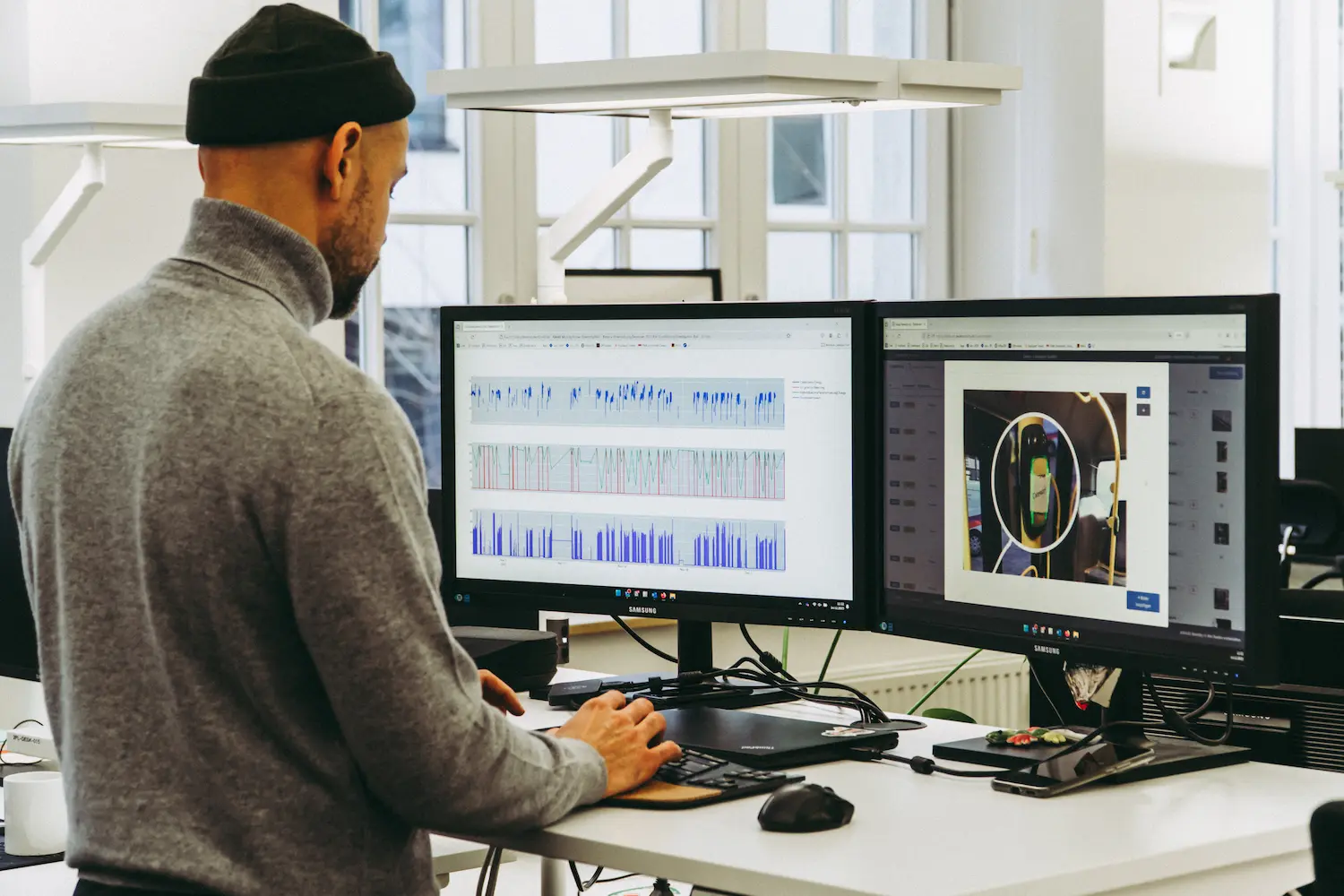
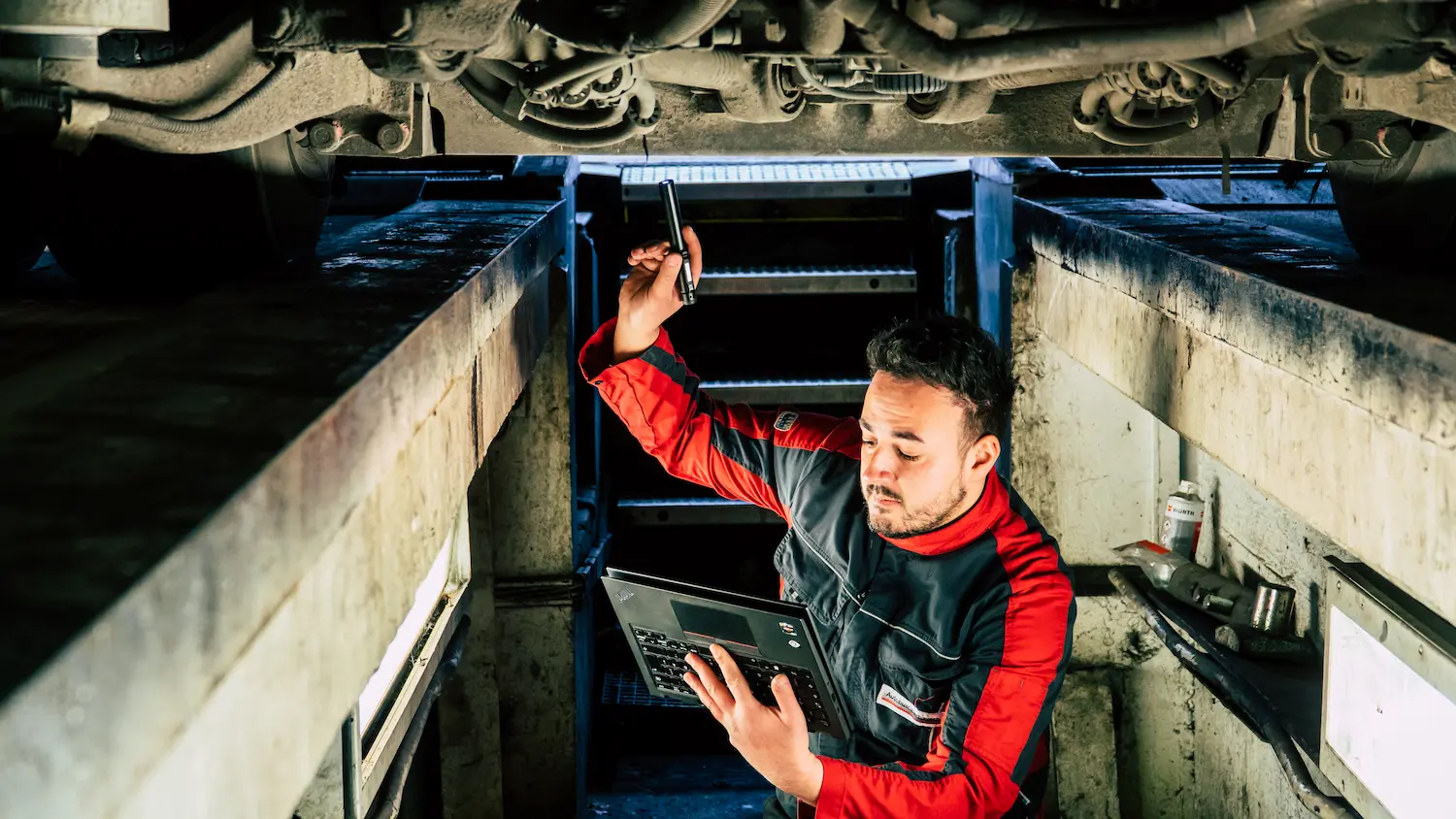
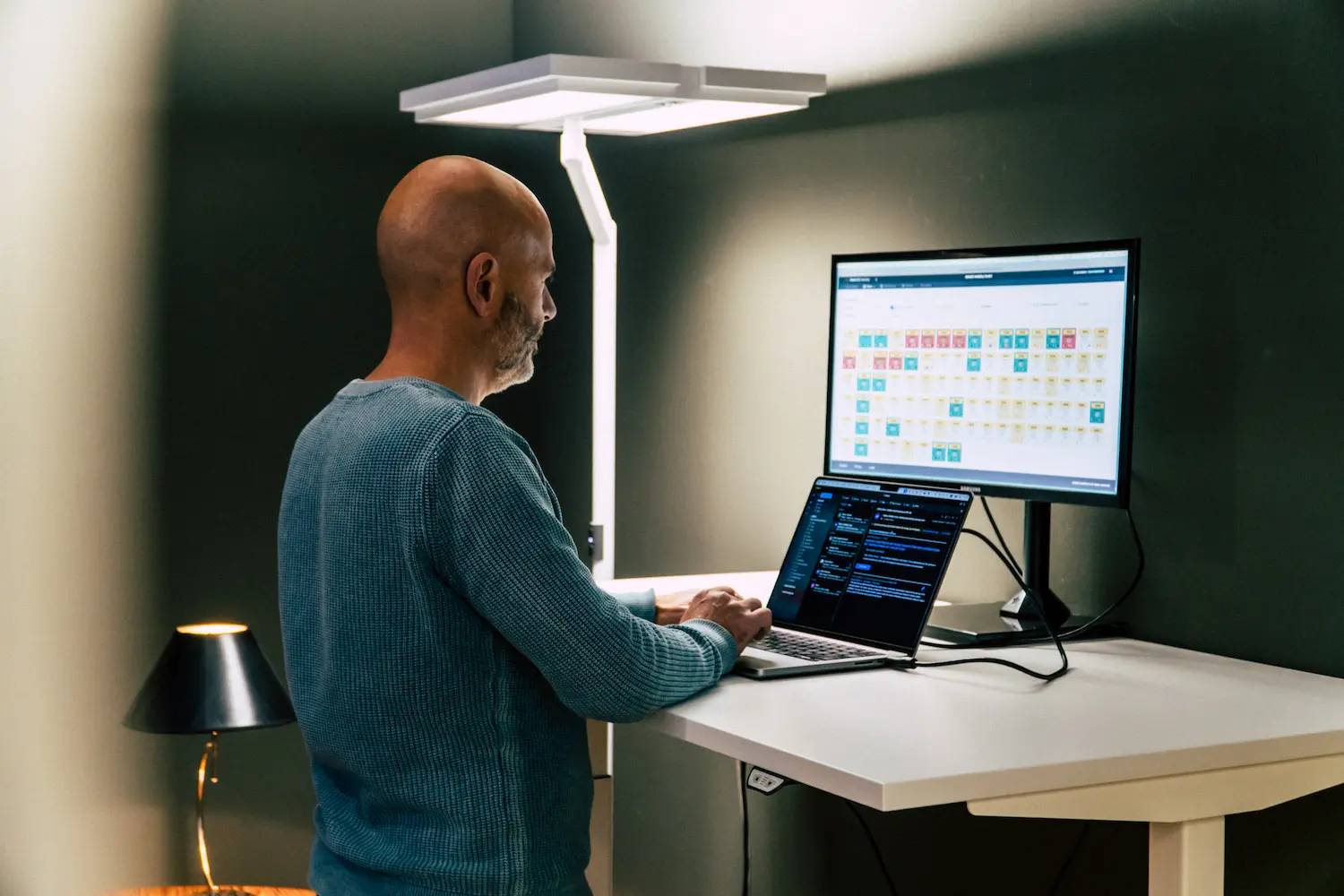
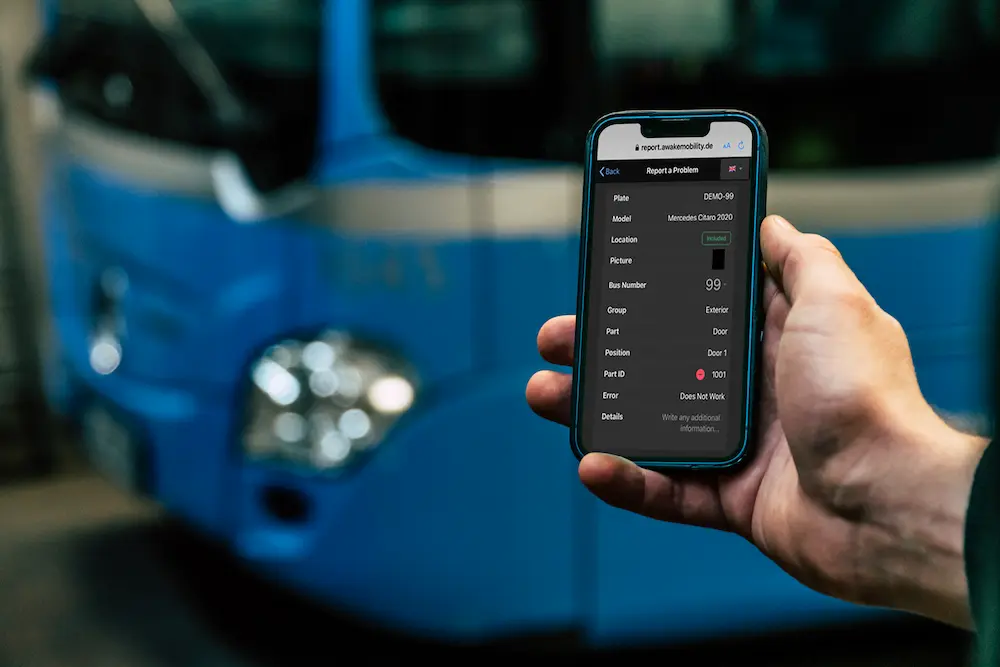
Trusted by leading mobility providers
Autobus Oberbayern has significantly minimized vehicle downtime since the implementation of AWAKE Mobility's solution in 2021. As the esteemed technology partner for Autobus Oberbayern, AWAKE Mobility has been actively engaged in advancing and enhancing the company's operational processes.
"The implementation of AWAKE Mobility's solution has helped to reduce our maintenance times and increases our vehicle availability."

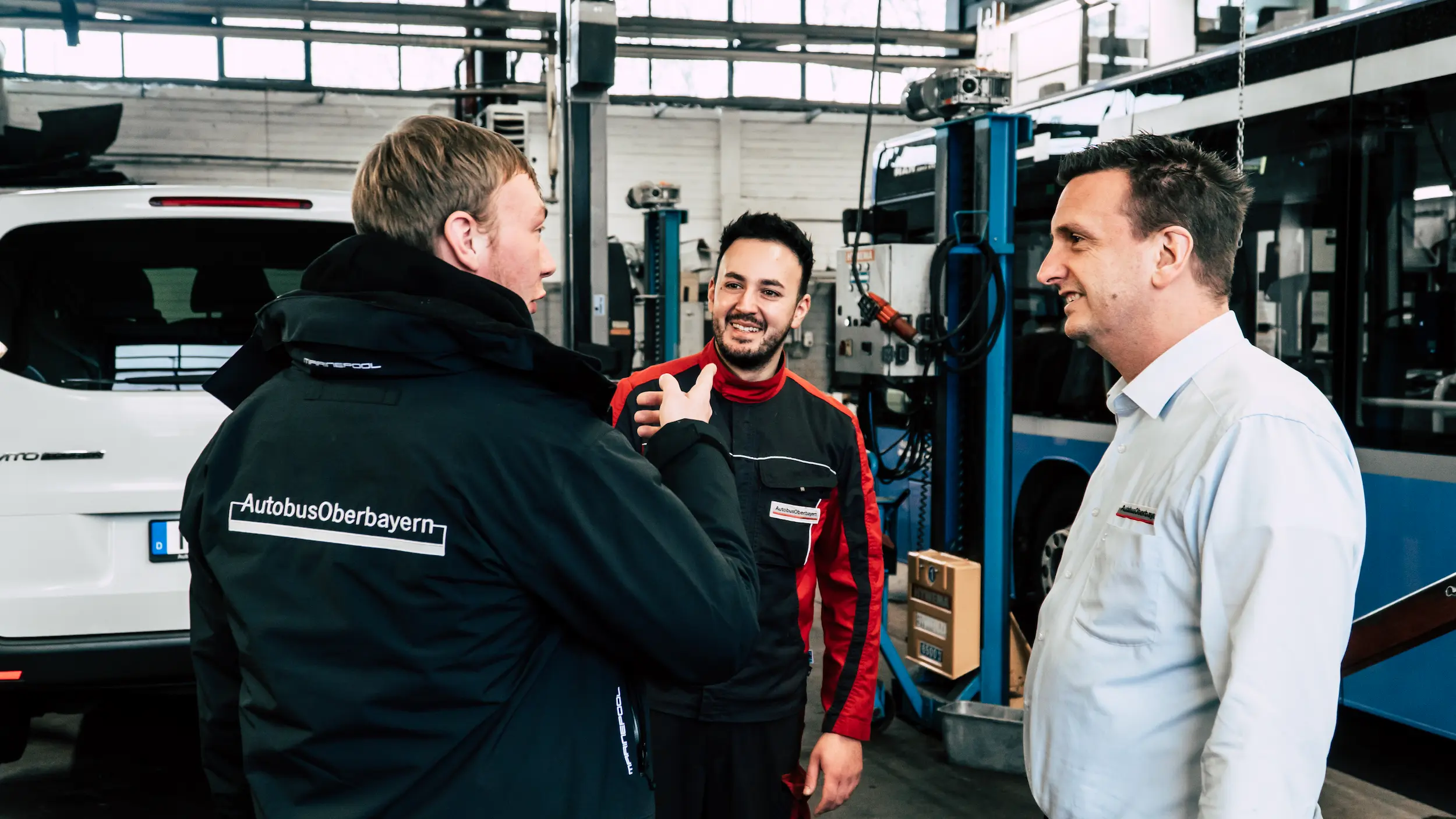
Implementation process for higher workshop efficiency
Our implementation process is swift and efficient. With dedicated support and reliable partnerships, we strive for seamless implementation, even in situations with constraints on time and human resources.
In our first call, we'll explore your main challenges and present tailored solutions to address them.
In our demo, we walk you through the platform, showcasing actionable insights from your vehicles.
Our hardware components are easy to deploy and our Customer Success team will support you in the set up and implementation.
Our customer success team helps set up and optimize your processes with our platform, addressing questions in regular sessions.
Get in touch with our team.
- Get a clear understanding of our solution in a 30 minutes call
- Explore the benefits of our platform for your use cases
- Understand what makes our solution unique
Frequently asked questions and answers
Yes, in contrast to most manufacturer solutions, AWAKE Mobility provides a multi-brand approach. It not only captures the basic FMS data points, but goes much deeper with remote OBD diagnostics as well as connections to several CAN-bus systems. All in all, our system provides the most vehicle data in the market and allows easy comparison between vehicle brands. No matter if you drive Mercedes, Setra, MAN, Iveco, Solaris or other brands, AWAKE provides you with the necessary insights required.
Our solution enhances workshop processes and improves the efficiency of workshop mechanics. Further cost savings can be achieved through the reduction of damages, spare vehicles, spare parts and vehicle replacements on the road.
Traditional fleet management systems collect data from the standardized FMS interface. FMS data is a limited set of data points which are provided to allow basic fleet management. AWAKE Mobility, however, does not only collect 200 times more data points through various interfaces, but interprets data and provides actionable insights. Additionally, the platform allows to digitize and automate entire end-to-end to processes such as maintenance interval planning or the communication regarding vehicle faults.
Predictive maintenance helps to plan for future technical problems. An artifical intelligence analyses the real-time health status of different components and alerts the mechanics if critical anomalies are detected. This allows to order the right spare parts and plan for maintenace just before a technical problem would interrupt the operations.
Every manufacturer provides a proprietary OBD-diagnostics computer which allows to diagnose error codes of their own vehicles. This requires the bus to visit the workshop in order to be connected to the computer. Remote diagnostics on the other hand, allow to read out error codes remotely. While remote diagnostics identify current faults, predictive maintennace goes one step further and predicts future technical problems. These problems can be pre-identified through continous AI-analyses of raw sensor data.
Explore all use cases of AWAKE Mobility
Smart decisions require information. AWAKE Mobility is your partner for vehicle data collection and analysis. Our web-based solution integrate seamlessly into your daily processes and accelerate operational efficiency.